Air Header
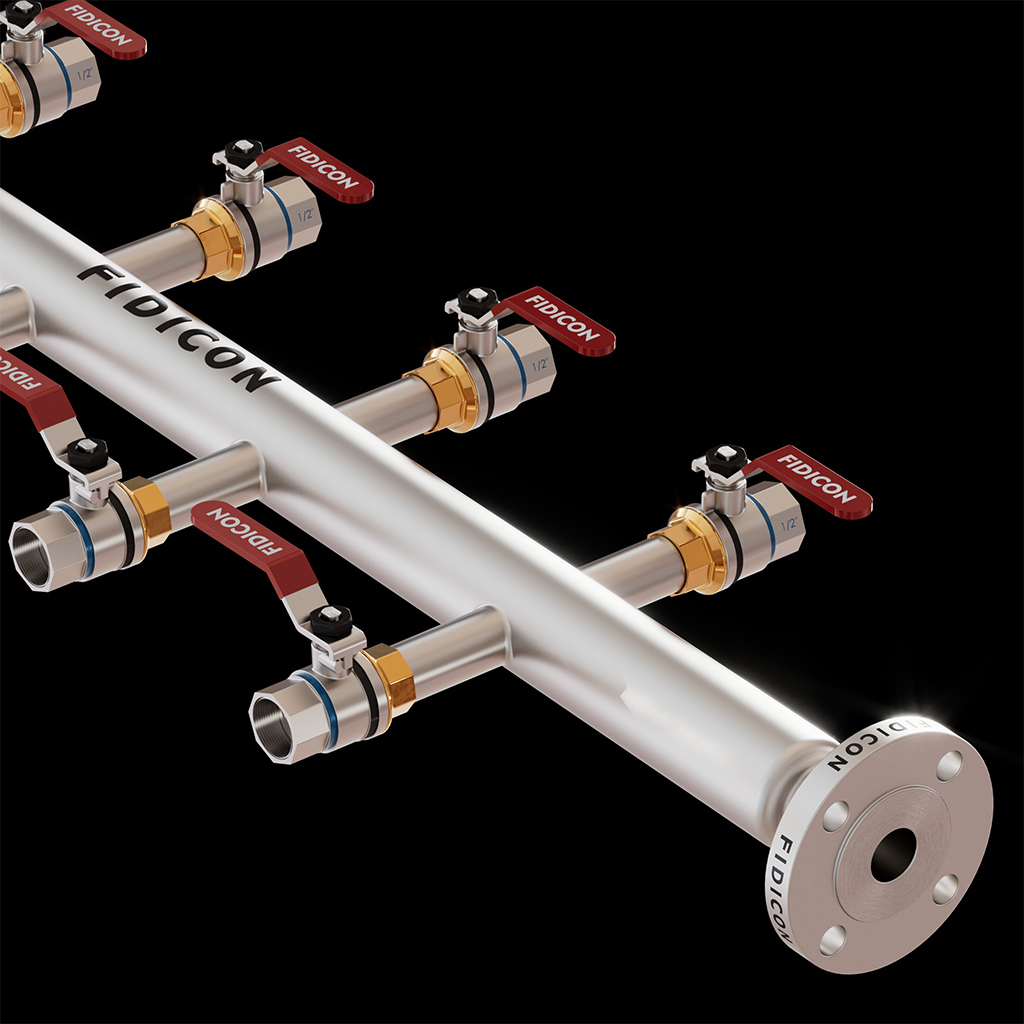
Air Header Manufacturer
Air Header is a unit mainly used to distribute & control compressed Air from one Inlet to Multiple Outlets for use in Plant or facility. It is most commonly used for distribution of Instrument compressed air within the plant for various utilities.
Air Header Introduction
An air header is a piping device designed to pressurize air and then distribute the pressurized
air to a variety of destinations or instruments in a process or industrial system. It is a manifold
and can have one inlet connection with multiple outlet connections.
The Important Facts in the Introduction:
1. Purpose:
Applied to supply pneumatic tools or valve controls with compressed air using a single compressed air supply line.
2. Design:
Usually comprises a central pipe (header) having multiple outlet ports, each fitted with a control and isolation valve.
3. Material:
Usually manufactured in stainless steel, carbon steel, or aluminum based on the application and environment.
4. Installation:
Installed vertically or horizontally in control panels, close to instruments, or on the pipe racks.
5. Application Areas:
Very common in the refineries, chemical plants, power plants, and other industrial automation systems that require a consistent air supply.
Air Header Characteristics
An air header is a small and efficient air distribution system that is widely applied in industries to distribute compressed air to different instruments or equipment. The following are the most important features:
1. A variety of outlet ports
With multiple outlets, which usually have needle or ball valves, to provide air to various instruments or control devices at once.
2. Single Inlet Design
A single inlet connection enables the distribution of compressed air present in a main supply line effectively.
3. Durable Construction
Composed of strong materials, e.g., stainless steel, carbon steel, or aluminum, which offer a great deal of resistance to pressure, corrosion, and high temperatures.
4. Space-saving and Compact
Compact, can be easily mounted in control panels, skids, or pipe racks where space is limited.
5. Easy Mounting and Installation
It has wall or panel mounting brackets or holes that make it convenient and stable to mount.
6. Pressure Tested
The pressure test is usually conducted on each unit to check that it does not leak and that it can operate reliably during working conditions.
7. Customizable Configurations
Can be provided in different sizes, numbers of outlets, and types of valves (needle, ball, etc.) depending on use requirements.
8. Maintenance Friendly
Easy design enables easy inspection, replacement of valves, or cleaning without considerable impact on the system.
Air Header Pressure Rating
An air header pressure rating is determined by the type of material, design standard, and valves and fittings used. But typical industrial headers of air can be in the following pressure ranges:
Typical Pressure Ratings:
Material Standard Pressure Rating
Stainless Steel (SS 304/316) Up to 6000 psi (approx. 414 bar)
Carbon Steel Up to 3000–5000 psi (approx. 200–345 bar)
Aluminum Up to 150 psi (approx. 10 bar) — less common
1. Application-Specific Rating:
A pressure rating should always be chosen in reference to the actual system pressure and margin of safety.
2. Connection Type Effect:
The pressure tolerance is also dependent on the connection type (e.g., NPT, BSP, welded, or flanged).
3. Design Standards:
A lot of air headers are made according to the following norms:
ASME B31.1 / B31.3 ANSI/ASTM PED (Pressure Equipment Directive)
4. Testing:
To ensure safety, air headers are normally hydrotested at 1.5 working pressure.
Air Header Temperature Rating
The material of construction of an air header is the most important factor in determining the temperature rating of the header and also the fittings and valves on the header. The general guidelines are as follows:
Normal Temperature Ratings by Material:
Material Temperature Rating (Approx.)
Stainless Steel (SS 304/316) -196°C to 400°C (–320°F to 752°F)
Carbon Steel –29°C to 425°C (–20°F to 797°F)
Aluminum -20°C to 120°C (–4°F to 248°F)
Key Considerations:
1. Valve Type:
The valves that are fitted to the air header (e.g., needle or ball valves) should also be rated to the same temperature range.
2. Sealing Material:
The maximum temperature rating can be restricted by internal seals (PTFE, Viton, etc.) in the valves.
3. Installation Environment:
Ambient temperature: in outdoor or hot-heat locations, such as refineries or boiler rooms. Recommended Steps of Disposal:
1. Decommission Safely
Compound the air supply and depressurize the system completely.
Safely disconnect all the inlet and outlet connections.
With the help of suitable tools and PPE, detach the air header by detaching it from the mounting structure.
2. Clean Thoroughly
Blow the air header out to get rid of any remaining air, oil, or contaminants.
Neutralize or clean in the case of systems exposed to hazardous media as per material safety data sheets (MSDS).
3. Material Identification
Determine the type of material (e.g., stainless steel, carbon steel, or aluminium).
Sort through recyclable and local waste laws.
4. Recycling Where You Can
Stainless steel and carbon steel parts can be taken to metal recycling centers.
Metal valves and fittings can also be reused or recycled.
5. Properly dispose Non-Recyclables
Otherwise, seals, gaskets, or plastic elements are to be disposed of as industrial non-recyclable waste.
Comply with local municipal or hazardous waste.
6. Documentation (where necessary)
In the case of industrial sites, keep the disposal records according to ISO 14001 or other environmental compliance requirements.
FAQs
An air header is a kind of manifold, which is used to distribute compressed air from one supply source to several instruments or devices. It usually has one inlet and several outlets, which
enable it to distribute air efficiently in industrial systems.
Air headers are often applied in oil & gas, chemical plants, refineries, and power plants to distribute compressed air to control valves, actuators, or pneumatic instruments.
Stainless steel, carbon steel, or aluminum is normally used to make air headers, which are chosen depending on the environmental condition and pressure needs.
An air header operates by receiving compressed air into the inlet port, where it is distributed equally to the various outlet ports, which are connected to various devices, providing a stable and centralized air supply.
• Makes air distribution to various devices easy
• Lowers the number of piping and leak locations
• Space saving during installation
• Enables centralized control and maintenance
An air header is a manifold that has only one inlet point of compressed air but has several outlet ports. It also supplies the compressed air to the different connected instruments, like control valves or actuators, in a manner that each of them gets a reliable air supply.
No, an air header does not control pressure. It merely dispenses compressed air. The pressure control is normally managed by the use of pressure regulators, which are installed upstream or at specific instrument connections.
Yes, it is possible to use all the outlets simultaneously; however, the supply pressure and flow rate must be high enough to cover the needs of the instruments connected to it without pressure loss.
All outlets typically have a needle or ball valve so that operators can isolate, control, or shut off air supply to individual instruments during maintenance or emergency.
When one outlet is blocked or shut down, the rest of the outlets do not stop working. The obstruction does not interfere with all the instruments attached to the particular outlet.
An air header is an air distribution manifold that supplies compressed air to various instruments or equipment throughout a system and is fed by a single source of compressed air.
Air headers are normally supplied with 4, 6, 8, or additional outlet ports depending on the demands of the system. The figure is adjustable to suit the requirement.
Air headers are usually fabricated using stainless steel (SS304/SS316), carbon steel, and aluminum, depending on the conditions of use, such as pressure, temperature, and corrosion hazard.
Yes, air headers of corrosion-resistant material, such as stainless steel, are most suitable in indoor and outdoor industrial settings.
Yes, individual air header outlets typically have a needle or ball valve that isolates or controls the flow of air to the instruments to which it is connected.
Yes, the majority of air headers, which are manufactured of stainless steel, carbon steel, or aluminum, could be recycled in authorized metal recycling centers with due cleaning and
disassembling.
Absolutely. The air header should be well washed to eliminate remaining air, oil, or contaminants, particularly when it was utilized in systems that deal with hazardous or corrosive materials.
As per the local environmental regulations, seals, gaskets, and plastic fittings should be separated and disposed of as industrial non-recyclable waste.
In the event that the air header was in contact with toxic or hazardous substances, then it should be considered hazardous waste and must be disposed of by a certified hazardous waste management agency.