Variable Area Flowmeters
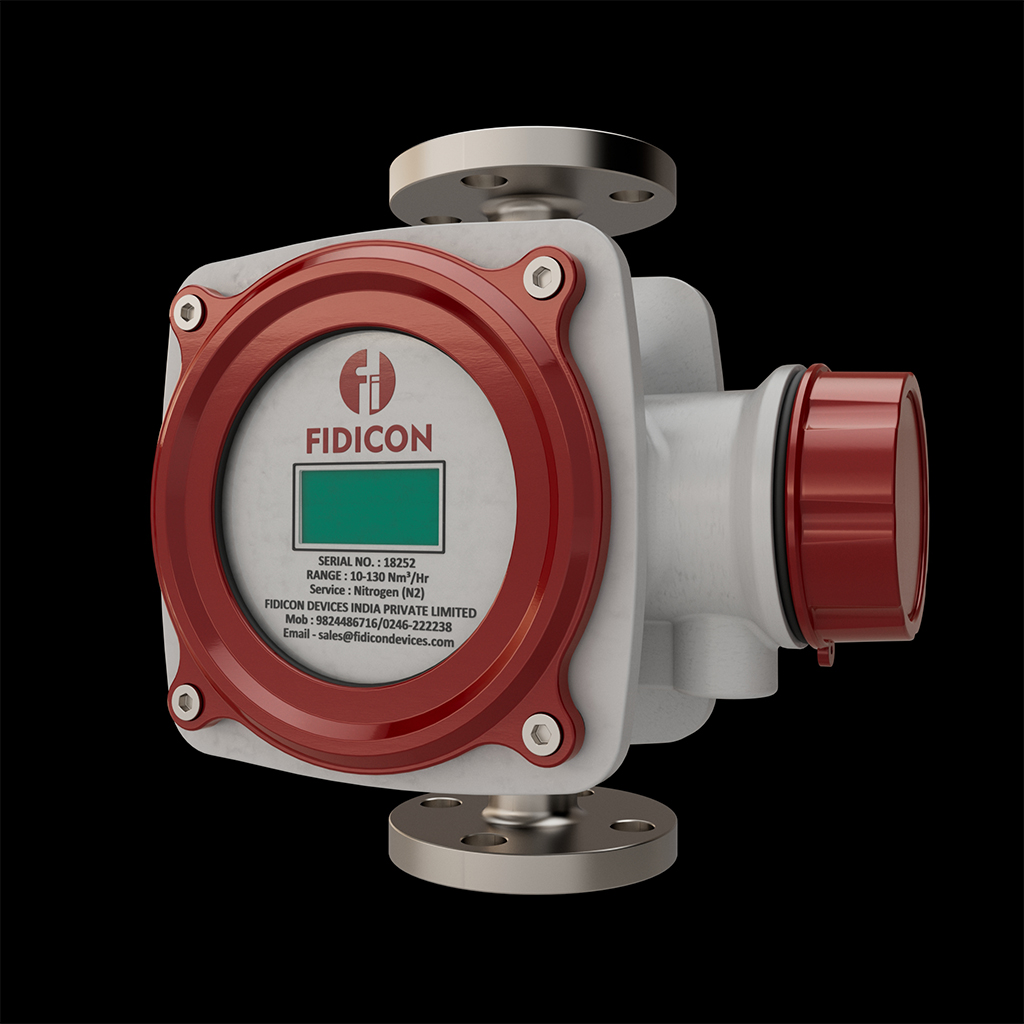
Variable Area Flowmeter Manufacturer
A variable area flow meter is a type of differential pressure (d/p) flow meter. Variable area flow meters are simple and versatile devices that operate at a relatively constant pressure drop and provide flow measurement of liquids, gases, and steam.
The variable area flow meter is popular for industrial flow indication because it has a linear scale, a relatively long measurement range, and low pressure drop – and they are quite simple to install and maintain.
The variable area flow meter’s operation is based on the variable area principle: fluid flow raises a float in a tapered tube, increasing the area for passage of the fluid. The greater the flow, the higher the float is raised. The height of the float is directly proportional to the flow rate. With liquids, the float is raised by a combination of the buoyancy of the liquid and the velocity head of the fluid. With gas flow, buoyancy is negligible, and the float responds to the velocity head alone.
Introduction to Variable Area Flow Meter
One of the most common devices is a variable area flow meter that measures the volumetric flow rate of fluids, e.g., a liquid or gas, carried by a pipeline. It is constructed upon a simple and very useful principle: that as the flow is greater, the area to which the flow is open is greater, and the rate of the flow may be determined with accuracy and directness.
The most common type of variable area flow meter is referred to as a rotameter and is made up of a tapered tube and a float. When the fluid flows up the tube, it pushes the float up to a level where the downward gravitational force on the float is offset by the upward force on the float exerted by the fluid. The position of the float then indicates the flow rate.
Variable area flow meters have the advantage of being reliable, easy, and visually indicating flow. They require no external power and are therefore applicable in low-cost, low-maintenance applications in most industries, such as chemical processing, water treatment, pharmaceuticals, and gas distribution.
A variable area flow meter operates in accordance with the principles of fluid dynamics, in which the flow rate of a particular fluid is determined by the position of a float placed within a vertically mounted tapered tube.
As the fluid is added to the meter at the bottom, it climbs up the tube. The tube contains a float that is free to move up and down along with the fluid. The faster the flow rate, the more force that acts against gravity to push the float. The tube is widened at the top; therefore, the higher the float rises, the greater the space becomes to enable the fluid to flow around the float.
What is a digital meter in a variable area flow meter?
A Variable Area Flow Meter (VAFM) has a digital meter, which is an improved form of the conventional flow meter, using the mechanical system of the float-based measurement with the addition of electronic sensors and a digital readout to provide a more accurate, readable, and higher-range flow measurement.
As opposed to solely using the visual observation of the position of the float, a digital VAFM contains electronic sensors (e.g., magnetic, optical, or ultrasonic sensors) to sense the position of the float. This information is then translated to digital flow readings that are displayed on an LCD or LED display built into the apparatus.
Important characteristics of a digital variable area flow meter:
Digital Display: Displays the flow rate in real time, totalized flow, etc.
Sensor Integration: Electronic detection of float position to measure the same.
Output Signals: Outputs analog (e.g., 420 mA) or digital signals (e.g., Modbus) to allow the system to be integrated or automated.
Data Logging: The flow data of the past is recorded in some models to monitor or report.
Remote Monitoring: Is able to be connected with PLCs or SCADA systems.
Benefits of Variable Area Flow Meter
Easy Design and Usage
The construction of variable area flow meters is simple and mechanical, with few moving parts. This renders them simple to use and comprehend with no complicated controls or electronics.
No external power needed (in case of analog versions)
A large number of variable area flow meters, particularly the more conventional rotameters, need no electricity to work and thus are suited to remote or non-electrified areas.
Visual Flow Indication
The float location in the transparent tapered tube gives an immediate visual read of the flow rate and is particularly convenient for on-site monitoring.
Broad Scope of Applications
VAFMs are applicable in most industries (water treatment, chemical processing, pharmaceuticals, and food production) to measure the flow of liquids, gases, and steam.
Cost-Effective
Variable area flow meters are cost-effective compared to other flow measurement devices both in terms of cost of purchase and after-sales services.
High accuracy in a wide range of applications
Although VAFMs are not the most accurate at very low or high flow rates, they are accurate enough (normally within 2% of full scale) to be used in general industrial and commercial applications.
Low Maintenance
They have fewer parts, are ruggedly constructed, and thus require less frequent servicing and have a long service life, particularly where the fluid is clean.
It Comes in Various Materials
VAFMs come in a variety of materials, such as glass, plastic, stainless steel, and PTFE, and can be used in corrosive environments or high-temperature or high-pressure environments.
Disadvantages of Variable Area Flow Meter
Only Vertical Installation
Variable area flow meters need to be mounted vertically to provide accurate readings, as they depend on gravity to make the float sit in the right position.
Not Suitable to Pulsating Flow
They do not work well in pulsating or unsteady flow conditions, and this can lead to erratic movement of the floats and inaccurate readings.
Narrow Pressure and Temperature Range
Most models (particularly those with plastic or glass tubes) are not able to accept high pressure or temperature and so cannot be used in extreme conditions.
Human Error and Manual Reading
Most of them are not automated and only need to be read manually, which may result in observer error or inconsistency.
Does not suit opaque or dirty fluids.
When the fluid is not clear, dirty, or contains solids, it may cover the float or block the tube, decreasing accuracy and reliability.
Key Applications:
Chemical and Petrochemical Industry
Applied in the management of the flow of corrosive fluids, acids, and solvents in chemical processing lines, it maintains safe and controlled reactions.
Water and wastewater treatment
Assists in the control and measurement of clean and treated water flow, the dosage of chemicals, and observation of the filtration systems.
Pharma and Biotech
Perfect to measure sterile and clean fluids in controlled conditions in drug formulation, fermentation, and cleaning of equipment.
Food and Beverage Industry
Used in clean-in-place (CIP) systems and to track the movement of ingredients, flavorings, and carbonated gases such as CO₂.
HVAC Systems
Applied in controlling the movement of air, chilled water, and refrigerants in the heating, ventilating, and cooling systems.
Oil and Gas Industry
Gas monitoring and fuel injection rates at upstream and downstream processes, including lubrication systems.
Labs and Research Centers
Often applied to experimental arrangements to determine the flow rates of gases, air, or small quantities of liquids in an accurate and visual way.
Industrial Gas Supply Systems
Confirms proper gas delivery in welding, cutting, and gas distribution systems.
Environmental Monitoring
Applied in a sampling system to quantify the flow of air, emissions, or pollutants during environmental research.
Automotive and Aerospace Testing
Applicable in coolant and fuel flow measurement during testing and performance of the engine.
Variable Area Flow Meter Technical Specifications
The common technical parameters that determine the performance and appropriateness of a variable area flow meter in a particular application are
The Range of Flow Rate
Measurement Range: Commonly obtainable between a few milliliters per minute (mL/min) and several thousand liters per hour (L/h) of liquids or normal cubic meters per hour (Nm³/h) of gases.
Example: 10 100 L/h (liquid) or 0.1 10 Nm³/h (gas)
Operating Pressure
Most VAFMs work to 10 bar (145 psi).
High-pressure models are able to work with pressures of up to 400 bar, depending on the material of construction.
Operating Temperature
Standard models: up to 120°C
Special versions made of metal tubes or materials capable of high temperatures can resist temperatures of up to 250°C and above.
Accuracy
Usually within 1 to 2 percent of full-scale reading.
The accuracy is subject to float design, calibration, and flow conditions.
Construction Materials
Tube: Polycarbonate, Glass, Stainless Steel
Float: stainless steel, PTFE, aluminum, glass
End fittings: SS304, SS316, PVC, etc.
The selection of the material is based on the compatibility with chemicals and conditions of the processes.
Connections
Common end connections: Threaded (BSP/NPT), flanged (ANSI/DIN), or compression fittings
Available sizes: Quite often between 1/4 and 2 inches, depending on the capacity of the flow
Mounting Orientation
It should be mounted in an upright position with the fluid rising upwards.
Output Options (Digital Models)
Analog signals: 4-20 mA
Digital communication: HART, Modbus (optional)
Alarm switches: High/low flow limits
Calibration
Flow meters are calibrated on a fluid basis, temperature, pressure, and orientation.
Quality assurance is frequently offered in the form of calibration certificates.
Recommendation on Disposal of Variable Area Flow Meter
The disposal of a variable area flow meter must be done in a controlled way by considering safety, environmental, and regulatory standards. It can prevent harmful environmental effects and enable compliance with the local waste management policies.
Disconnect and Decontaminate
Ensure that the meter has been completely detached from the process line prior to disposal.
Clean and decontaminate all sections in a way that there are no chemical remains when it is to be used with hazardous or toxic materials.
Disassembly Material Separation
The variable area flow meters with glass tubes, metal floats, plastic components, and rubber seals are common.
Separate such materials as much as possible:
Glass tube: Treat carefully; in some places it can be recycled.
Parts made of metal (stainless steel, brass, aluminum) → Sell to the metal scrap or recycling centers.
Polymer or plastic parts -> Dispose of them in the garbage in accordance with the local plastic waste regulations.
Deal with Hazardous Components.
If the meter contained radioactive or chemically polluted materials, it may be considered a hazardous waste.
Inquire of the authorized waste management agencies on the way to dispose of it.
Adhere to the local environmental legislation.
The instruments and industrial wastes must be disposed of as per the local government or the industrial disposal norms (such as CPCB, EPA, etc.).
Reuse or Recycling
Repairable or functional parts can be
Re-calibrated and reused
Replaced by a new one and sent back to the manufacturer to be recycled or refurbished (supposing the supplier has a take-back program)
FAQs
Variable area flow meter (VAFM) is a type of flow meter used to measure the flow of either liquids or gases. It is based upon the fact that the more the flow, the more the area of flow, and a float or indicator may be made to rise through a tapered tube as far as to show the rate of the flow.
It operates by offsetting the force of the upsurge of fluids in a tube and the force of gravity down on a float. The float is lifted up to a position where these forces are equal by increasing flow, and the flow rate is then read on a scale.
Liquids and gases such as water, air, steam, chemicals, and fuel can be used in VAFMs so long as the fluid is clean and not viscous and the system is not exposed to pressures or temperatures in excess of those that the meter can absorb.
It consists of the following important elements:
- A narrow tube (made of metal or glass)
- A float, which swells and falls with the stream
- A reading gauge or scale of flow rate
Optional: electronic output transmitters or sensors
They find application in chemical processing, water treatment, pharmaceuticals, food and beverage, HVAC, and laboratory testing, anywhere that it is desirable to measure flow inexpensively and reliably.
The flow range is dependent on the model.
- Liquids: 10 mL/min – several thousands of L/h
- Gases: 0.1-100 Nm³/h
Specific ranges depend on the kind of fluid, pressure, and meter size.
- Pressure: Up to 10 bar on a standard meter and up to 400 bar at high pressure.
- Temperature: Common models are rated from -20 to 120°C, and special models up to 250°C or above.
- Tube: Glass, stainless steel, or plastic (e.g., polycarbonate)
- Float: Stainless steel, PTFE, aluminum, or glass
- Fittings: Brass, stainless steel, or PVC depending on the chemical compatibility
Accuracy is usually +/- 1 percent to +/- 2 percent of full scale, depending on calibration, design, and flow conditions. Even more precise models may be tolerated even more closely.
Common forms of connection are
- Threaded (BSP/NPT)
- Flanged ANSI/DIN
Compression fittings
They come in different sizes ranging between 1/4 and 2 inches, which are made to suit the application.
- Easy and inexpensive structure
- No external source of power needed (mechanical models)
- Visual flow indication
- It can be used with liquids and gases
- It is simple to set up and repair
Not necessarily. Mechanical VAFMs need no power and are therefore suitable where power is unavailable or in remote locations. Digital or electronic versions, however, can require power to drive the signal or monitor remotely.
- Not as precise as the sophisticated electronic flow meters
- Has to be mounted vertically to work properly
- Unsuitable to opaque, highly viscous or particle-laden fluids
- The pressure and temperature changes can affect the readings
Unless they are made to withstand such conditions. Standard VAFMs are limited to moderate pressures and temperatures, though metal tube models can be designed to take higher pressure and temperatures with suitable materials.
Indeed, particularly when they are fitted with transmitters or alarms. But in high-precision control or automated control, electronic flow meters may be more appropriate.
Make sure the meter is disconnected and empty of any process fluids before disposal. Next, separate recyclable items such as metals and plastics and discard them following the local environmental laws.
Yes. There are numerous parts that can be recycled, including stainless steel floats, metal fittings, and glass tubes. Nevertheless, verify with recycling centers in your area to make sure they take such materials.
As a rule, they do not have any dangerous substances. However, when they were applied to corrosive or toxic fluids, they must be decontaminated before disposal so as not to degrade the environment.
No. It is better to dispose of the glass tube somewhere in the industrial or laboratory glass waste systems, as it may cause injuries and pollution.
Other manufacturers have programs that recycle or give back out-of-date equipment. Call the supplier and see whether there is such a program on your model.